
Unitop has recently developed Mechanical Vapour recompression (MVRE) for achieving Total Zero Liquid Discharge without using Steam or any external heat source.
An ISO 9001:2015, 14001:2015 & 45001:2018 certified company, Unitop Aquacare is a trusted name in the field of caustic recovery plant and zero liquid discharge system with more than 750 clienteles worldwide and a number of repeated orders. The company is one of the leading engineering firms with four decades of experience in caustic recovery and Zero Liquid Discharge systems for design, manufacturing, supply, installations and services. Unitop Aquacare Ltd is promoted by S M Mondkar, a chemical engineering graduate from IIT Mumbai, having experience of over 55 years in the process engineering industry. The company is now run under the able guidance of his son Ashish Mondkar, a mechanical engineer from Mumbai University. Speaking on the quality control and international certification, Ashish Mondkar in an interview with us, said, “All our manufacturing set-ups are ISO 9001:2015, 14001:2015 45001:2018 certified by TUV as well having fabricated & equipment under stringent standard of consultants like EIL, L&T, Toyo, TCE, Jacobs etc.

Our manufacturing setups are equipped with automated machinery to cater to our customer’s needs, ensuring quality. Our manufacturing system are approved/certified by international standard such as CE (Europe), SELO (China), NR13 (South America), EAC (Russia) and ASME Section VIII. On manufacturing facilities and fabrication capabilities: Ashish Said our manufacturing unit is spread over 2,00,000 sq. ft. and located in Mumbai & Gujarat. The fabrication, specialised QC and safety personnel are supported by skilled and semi-skilled labour enabling us to meet time bound deliveries and quality standards. With a view to add to the growing demand of Zero Liquid Discharge across all industries we have recently expanded to new Unit over a sprawling 28000 m2 large area in Umbergaon Gujarat hardly 140 km from Mumbai. Both these units together have a manufacturing capacity of up to 15 Evaporations plants every month.” “We have a professional team of over 60 engineers experienced in commissioning and supporting the clients,” added Ashish while speaking on aftersales service. “We have dedicated engineering staff to provide online support to our clients for their urgent requirements.” In fact, in the COVID period when mobility was a challenge, we still were able to successfully handover all our plants sitting right there in India, this itself is a testimony to our automation and service skills Says Ashish, “Quick delivery and efficient after sales service to our clients, irrespective of location have been our core focus and for that we have put lot of effects to impart technical training to our local representative’s/ channel partners as time is essence.
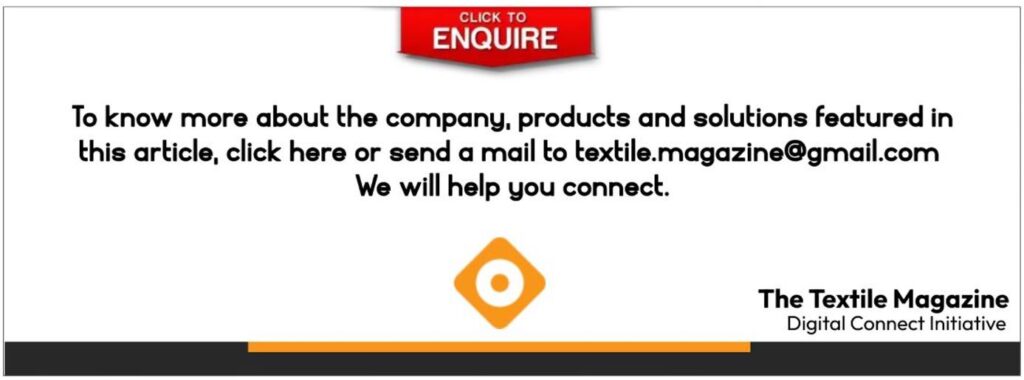
We have dedicated expertise available on call to attend to problem solving on phone itself. We are in constant process to become an Indian multinational doing the better things in simpler way.” He added that Unitop Aquacare has expertise to recover the caustic for denim and yarn dyeing mercerisation. “Waste caustic generated from this segment have lot of colour and size impurities and Unitop Aquacare with experience of over 40 denim caustic recovery has the largest know-how to make the recovered caustic reusable.” he said.
Advanced technologies and automation
Unitop Aquacare designs tailor-made systems to suit individual customer’s need and the local condition like quality of water, environmental impacts, space constraints, operational conditions, etc. Solution includes:
• Total one-touch operation plant involving minimum manual intervention
• MIS daily reports in real time or history charts or graphic
• Plant analysis and troubleshooting module
• Report alert on mobile or email
• Remote-controlled operations
• Mobile based service app, which helps customer to generate service call and to get solution faster.
Market presence

Unitop Aquacare have made deep inroads in the European, Chinese, Turkish Bangladesh and Indonesia markets. All the customers in this region were using either using European Equipment’s due to service comfort or quality, however since they have used our system, they find it much more convenient for the application. Based on our presentation on steam saving they prepared to change the system to our Evaporator saving a lot of money due to lower operational cost, user friendly operation, reliability of performance and good local after sales service. In fact, not just in India but Bangladesh, China, Indonesia, Thailand has an over 70 percent share of the market for Evaporator Ashish further quoted, “We have got business from clients who were traditionally European machinery buyers and this was possible due to superior technological advancements & low utility costs.” He adds, “We follow textile industry and our customers very closely. We identified that most of the textile are facing challenges to supply a constant higher-pressure steam to any machine for that matter Evaporator. We have optimised our design to operate our Evaporator at low pressure keeping in mind interest and benefit of customer. We are always focused to design Evaporator it operates at low steam consumption and I proudly say that we are around 15 to 20 per cent lower than European competitor. We do it in an innovative way by washing steam condensate to generate steam which is a heat source for preheating the feed.”
“Unitop is most admired & trusted company in the eyes of our global customers by understanding their rapidly changing requirements in water & waste water treatment by delivering world class innovative, cost effective, sustainable, quality products and prompt services, which are globally competitive & customer centric.”
New product development
MVRE
Mechanical Vapor Recompression (MVR) Evaporators are the Low Operating Cost Systems to treat the Textile Effluent/Wastewater without using any external heat source or steam. It is driven by electrical energy which is cheap & clean source of energy. MVR Evaporation is the most thermodynamically efficient process to concentrate Effluent/Wastewater streams or to achieve Zero Liquid Discharge (ZLD) in wide industries & applications including Textile, Pharmaceutical, Food & Beverages, Chemical, Paper, ETP & RO Reject etc.

Zero Liquid Discharge
Unitop Aquacare Ltd has now even started its Total Zero Liquid Discharge systems from Effluent Treatment Plants, Reverse Osmosis Systems to Evaporation and drying system to be able to recovery over 99% water and eventually offer client the salts in form of solid waste with hardly 10% moisture. This baggable salt can either be reused or taken to a solid waste disposal site. We are looking forward to support our customer to achieve the elusive Zero Liquid Discharge to be able to follow Pollution norms and help form cleaner world.
UAC 24
Grey merceriser/Yarn dyed merceriser contain a lot of impurities in form of dyes, starch, oil and wax. These impurities are repeatedly recycled then it makes the recovered caustic unusable. Unitop aquacare has a patented coagulation technology that can remove the colour impurities such as starch and other dark colours and size impurities such as Starch, wax, oil from caustic so that the recovered caustic has improved properties.
This has improved the recovery pace of caustic for these customers who otherwise were unable to use the recovered caustic.