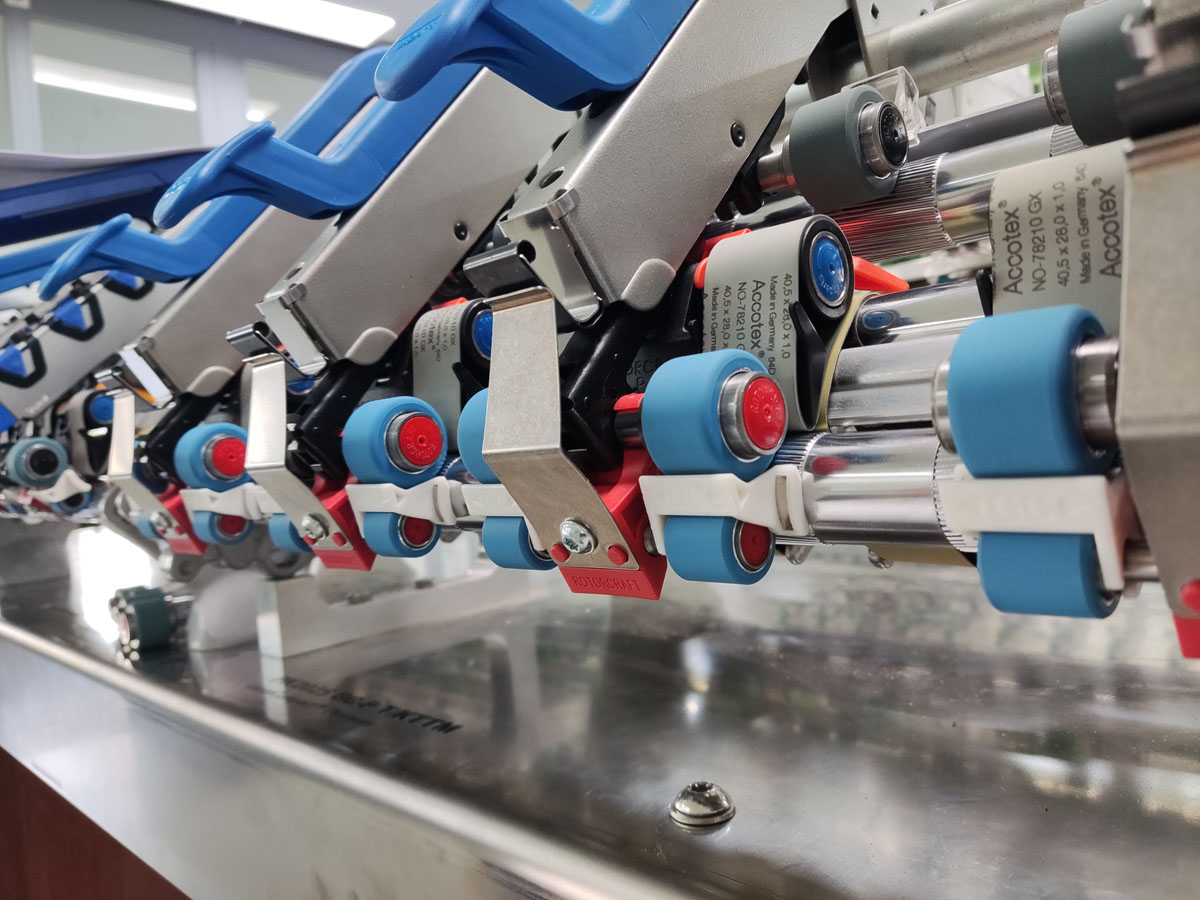
The third generation in compact spinning GreenCompact (GC) allows spinning mills to produce compact yarn at the cost of a normal ring yarn, has been well accepted by the industry. For valid reasons, ring spun yarn is considered the most universal all purpose yarn for the manufacturing of fabrics. Nevertheless, the ongoing search for improvements to staple fibre yarns presented the world’s textile industry with a new development.
The mechanical compacting solution GreenCompact offers superior quality properties compared to normal yarn, while production costs remain the same. It does not require suction, it uses only magnetic and mechanical features.
One of the latest innovations on the ring spinning market is the optimization of the spinning triangle in the fiber guide channel of the compactor. The fiber guiding channel has been individually optimized for the operation of coarse to fine yarn counts. An advantage that offers much less hairiness, increased strength and elongation. GreenCompact achieves superior results for coarser yarn counts up to Ne30 at a higher grade of energy-efficiency and substantially combined with less maintenance compared to suction devices.
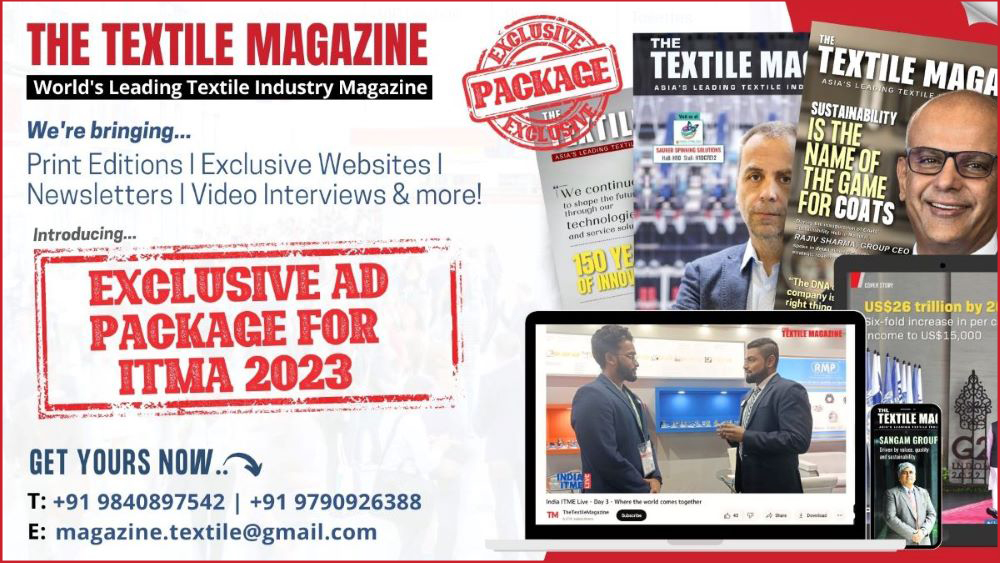
The GreenCompact execution can be fine-tuned precisely for every frame make and model using dedicated upgrade kits. Upgrade kits support your technicians to achieve a perfect spinning geometry with solid fiber control in the drafting system. Fine adjustment between front top roller and middle top roller can be ultimately controlled. The drafting zone and the compacting zone are matched to bring the fibers under equal tension for less yarn breaks.
If it comes down to drafting techniques Rotorcraft AG offers solutions such as traverse spinning and cross piecing ability. Particularly, the GC Traverse solution is user-friendly and does not require additional work staff, as only one additional component is required. When using the GC-traverse solution there are no quality losses involved – unlike to competitors concepts. As a benefit of GC traverse, the reversing interval of the rollers can be increased by at least two times. As a result, the grinding interval for the cots can be extended by factor 3. GC traverse can be equipped on all ring frames which already have an engine installed for traverse motion or can be run as stand-alone.
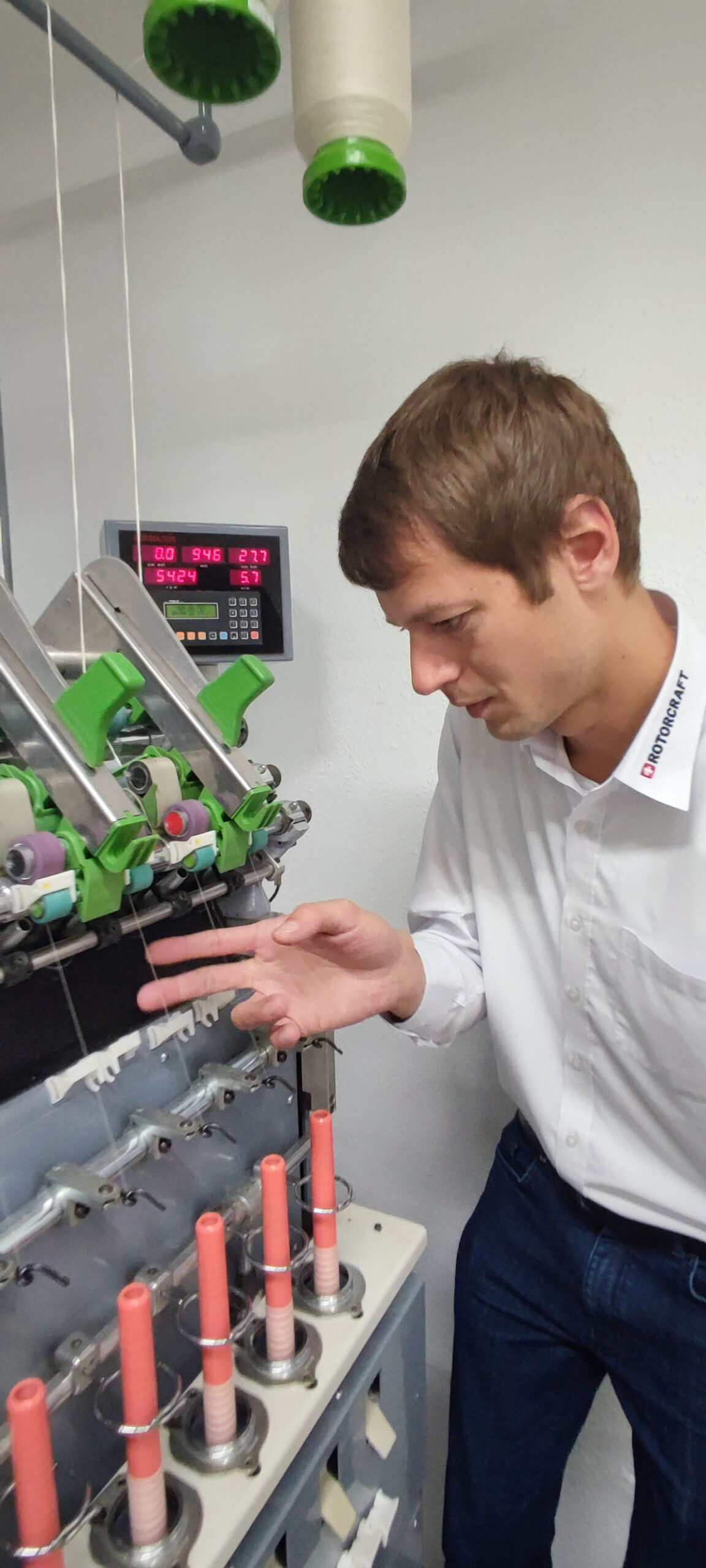
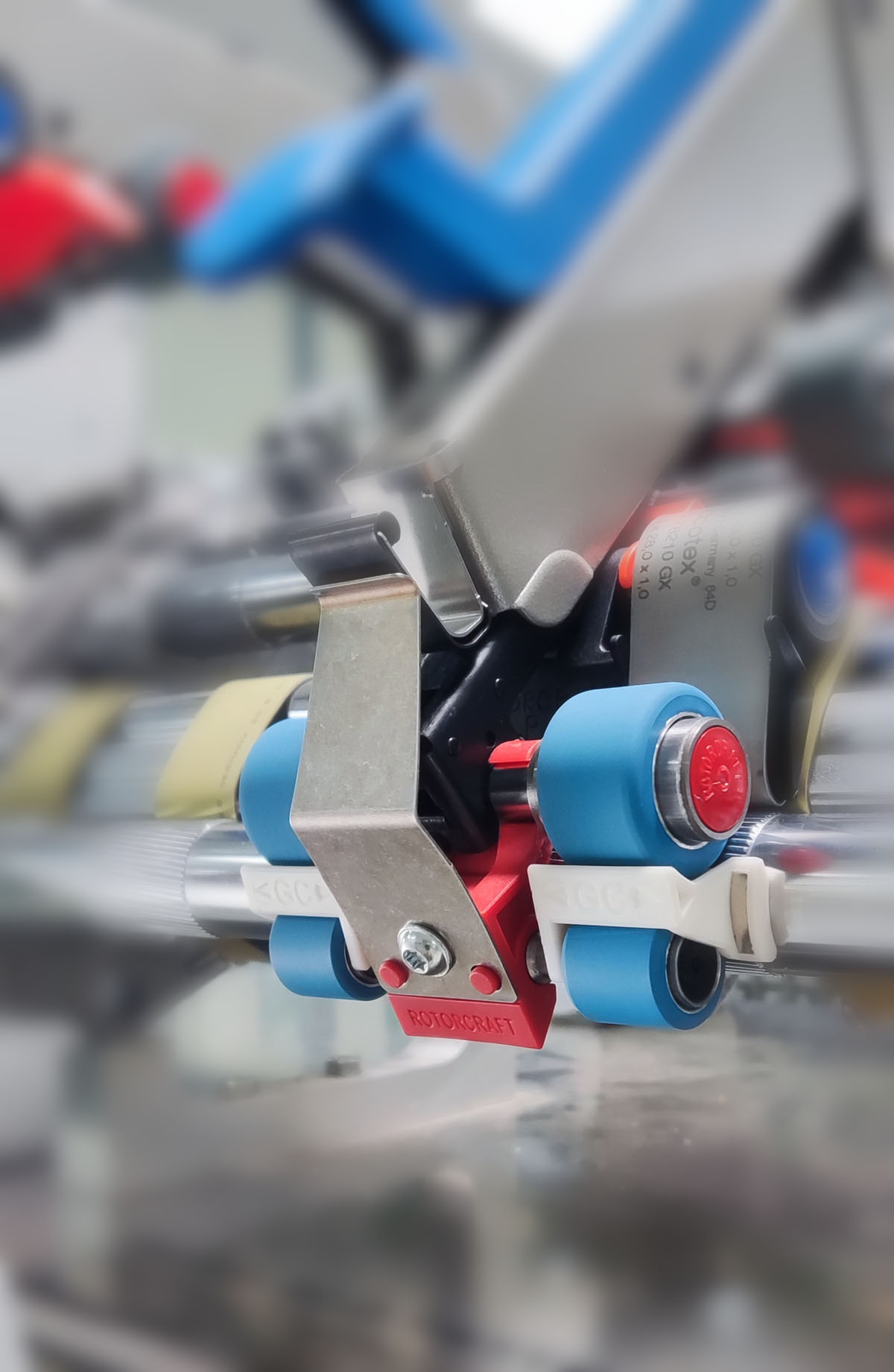
The GC SIRO upgrade kit opens up the field to produce twist yarns all in comfort of a safe and solid GreenCompact environment. Further developments regarding optimizations for 100% synthetic materials (MAA) are in progress.
There can be no doubt about mechanical compacting being the state-of-the-art technology and equipment for today’s ring spinning tasks. The future of compacting is GreenCompact.