The textile industry is known to exist for centuries. Even with new blends and trends in the market, it still retains its old cultural importance all over the globe. So what does a modern digital print industry want to do in the textile world? To revolutionize it? one company has decided to take up the mantle.
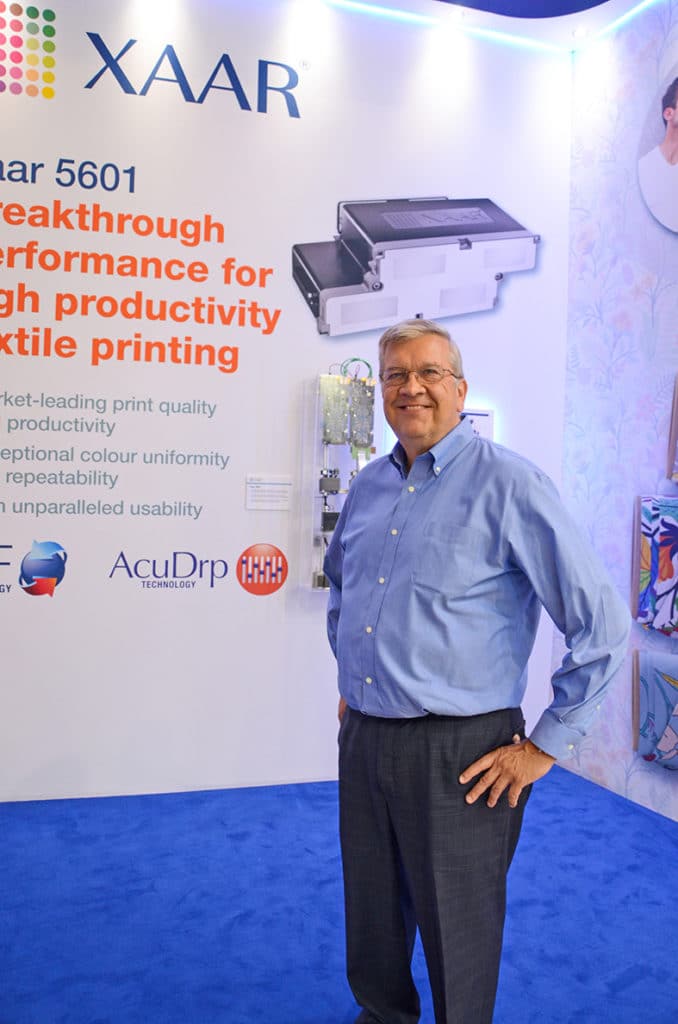
Xaar is the world’s leading independent manufacturer of piezo-based drop-on-demand inkjet printheads. It has been developing and manufacturing printheads for the last 29 years and continues to stay at the top of the game by being a pioneer of innovative technology in the industry. It has managed to create new trends in various industrial markets such as ceramics, wide format graphics, labels, and laminates. This time, its eyes are set on the textile world, and it is ready to enter it in style.
At Techtextil held in Frankfurt in May, we had the pleasure of meeting Mr. Michael Raymond, Sales Manager at Xaar. The group is now able to print on a much wider range of materials including fabric.
“We did not have the technology to work with the water-based type of fluids required for textile markets. But our new technology platform which is the Thin Film Piezo Silicon MEMS manufacturing technology allows us to,” said Mr. Raymond. This new innovation only expands Xaar’s ever-growing technology portfolio. Its 1201 Printheads, which are small drop thin film Piezo Silicon MEMS devices, are widely used in scanning type and lower end printers. The 5601 printhead is a lot more advanced. The printhead has a whopping number of 5680 nozzles and the ability to handle not one but two colors.
One printhead is capable of printing either single colour at 1200 dpi or two colour at 600 dpi. The ‘Z’ shape of the printhead allows you to make a wider printer without growing the depth of the printer. A smaller printer means one which is generally easier and cheaper to build.
The mechanical features and level of accuracy of these technologies is indeed commendable. In order to fix the issue of stitching these printheads together, the developers at Xaar decided to make four rows of nozzles. When these printheads come together, the nozzles automatically line up. There is no mechanical adjustment required.
These printheads stand out even more from the rest thanks to the way they are made. In Xaar’s other printheads, nozzle walls and most of the actuators (where the nozzles are in the printheads) are made of a piezo material, with the channels manufactured using a micro-sawing technique. This is not the case with the Xaar 5601.
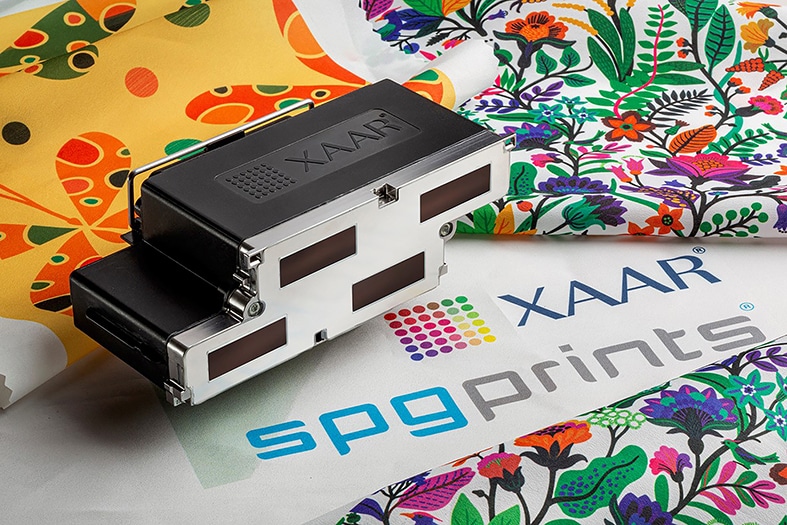
Xaar uses the Silicon MEMS manufacturing process, which allows it to make each and every individual actuators that are in these printers on Silicon Vapors, all at once, at the same time. With these printheads during installation, you can put in a printhead, run a test pattern for alignment and before you know it, using software to align the printheads your printer is up and running in less than 20 minutes, as compared to the many hours it takes for the machine to start running again on standard platforms.
The science behind the delivery of quality by Xaar’s products is fascinating. Another element incorporated is the Xaar TF Technology that keeps the ink circulating in the printer at all times. The ink flows past the nozzles, always bringing new ink into them. Circulating around the nozzles keeps them clear of any debris, air bubbles or other disturbances that could affect the print quality. This strengthens the printhead’s reliability and credibility even more.
Acudrp is another technology incorporated thanks to the Silicon MEMS process. With this, each nozzle is aligned individually on the printhead. “If you know anything about making printheads, each printhead has a velocity profile that may not match the next printhead. But with the Acudrp technology the print quality is much higher because banding and colour density variations are minimized,” said Mr. Raymond.
There are many other features under this exciting and innovative process, but how feasible is this new technology for those who would like to invest in it? The answer is ‘very feasible’. The Silicon MEMS route allows printers to be cheaper in the longer run. In this process, the greater the volume manufactured the higher the cost brought down. The printheads are also priced strategically against other technologies. As Mr. Raymond disclosed: “Kyocera printheads are considered the standard for almost 5-7 years now. Our printheads have twice as many nozzles as compared to Kyocera’s printheads. Our printer can handle two colors as well. So one of Xaar’s printheads is equivalent to two Kyocera printheads.”
This ultimately makes the highest priced component of a printer more affordable, thus reducing the cost of the printer and the printing process in the long run.
All of this has the potential to create an influential shift in the textile industry on a global scale, specifically the directive fabric and dye sublimation area. Dye transfers are limited to polyester type materials or blends. This makes widely used direct fabrics like nylons, silks and cottons inaccessible, thus limiting opportunities. Dye sublimation is used more often as it is a dry process. This makes it an easy space to control and enter. By introducing the digital printing market into the textile space, directive fabrics can be more effective as compared to dye sublimation, opening up avenues and options never explored before. Xaar’s collaboration with the majors like SPGPrints (5601) and D.Gen (1201) further proves that the manufacturing giant plans to take the future of both digital printing and textile together to newer heights.
I believe this internet site has got very excellent composed written content blog posts.
I like the valuable info you supply to your articles. I’ll bookmark your weblog and take a look at once more here regularly. I am quite sure I’ll be informed many new stuff right here! Good luck for the next!